A preamble
My foray into densitometry and meditation on the design and construction of densitometers is now approaching a decade-long anniversary. It is a very niche topic, one that would excite very few people and is largely irrelevant to the mass of film photographers, who are already a small niche of the much broader community, to which I feel I belong. My personal notes on the topic vastly outnumber (and literally outweigh) my musings on other photographic subjects, yet I struggle to assemble these thoughts into meaningful, useful texts. My intended series of articles on the design and construction of a densitometer has fallen so far behind from the actual work on the project, that I do not even possess the finished device any longer.
But… meanwhile… I stumbled into a project, which I feel can be wrapped up into a neat, complete write-up of educational and practical value to both technically-minded photographers and electronics enthusiasts. I hope such a write-up can also kickstart me creating a broader range of texts here…
Introduction: meet Macbeth
Last Christmas, amidst a deep-dive rabbit hole into reflection densitometry, I bid on a listing for a used “as-is” Macbeth TR-527 densitometer, not realizing it would ship from California. My holiday gift to myself arrived about a month later in Bulgaria, luckily well-packaged and “AS-WAS” in the listing - in one piece, with the original manual and warranty card, and hopefully somewhat functional:
It was a handsome beast(about 30lbs’ worth), with the usual wear-and tear of an instrument from the late 70s. I was pleasantly surprised how robust it was - all cast-metal construction, thick enamel paint, and a surprisingly flexible and well-preserved power cord.
The TR-527 is a very capable instrument, which has been used for rigorous sensitometric work (see Henry, Controls in Black and White Photography, 1983, p.29), with a claimed accuracy and repeatability of 0.02 OD units, which is plenty for my purposes. Henry uses the TR-524 model. The two units only differ by the measured spot size in reflection mode (approx. 3mm for the TR-527 and 5mm for the TR524). Both the transmission (TD) and reflection (RD) measuring heads include a 4-filter turret for quick measurement of visual and tri-color densities. Much later, I also found out in my reverse-engineering that Macbeth (and their parent company Kollmorgen Corp.) put a lot of effort in the design of this device to ensure ease of operation, stable readings, and long life. Features such as intensity-feedback lamp control and filter position memory were not immediately apparent but welcome discoveries as I dove deeper into the electronics, and will be discussed at length later. Both TD and RD measurements follow the ANSI standards of the time and the filters are standard Kodak/Wratten numbers, with known spectral transmission.
All great stuff. I was hopeful that a Macbeth calibration plaque or step wedge might be hiding in the ream of documents, which came with the unit, but alas. Luckily, all three transmission stage plates (1, 2, 3mm aperture size) were present, and at first glance, Macbeth had a good chance of being of sound mind and body and good for another 50 years of operation.
In depth
I bought the unit as-is, and the listing showed it powered-on with an illuminated display:
After investigating the power transformer and rewiring it for 230VAC operation, I was able to power and test the densitometer. However, it was quickly obvious that there would be more work to be done. The RD head did not illuminate and could not be activated, the “ZERO” buttons did not work, and although the transmission mode showed some response to different test densities, clearly there was work to be done on the inside.
As I went further into disassembly, I was confronted with a substantial challenge - no schematics for the TR-527 or any similar unit were available, either online or in print, and the electronics were more complicated than I had imagined. Five PCBs in card slots contained the majority of components, but there was a rat’s nest of point-to-point wiring connecting them, making tracing any connection very difficult. The base of the unit had a lot of dust ingress and there were odd signs of damage in select areas of the device. I was initially discouraged and kicked my feet for a couple of days, wondering how to proceed. I even considered gutting the 70’s electronics and replacing them with a modern, possibly microcontroller-based solution. But that would have been blasphemy. My curiosity and appreciation for discrete analog design won out in the end - I was determined to tear down the Macbeth to bare components, clean and restore the mechanical ones, and trace out the entire schematic. I made an honest effort to understand how the TR-527 worked and a few months later, I am satisfied (and relieved) to present a success.
Furthermore, it made sense to do justice to this wonderful analog device and draw up the schematic diagrams with pen and paper. Replacing the convenience of CAD for the rigor of drafting was a very enjoyable experience, albeit exponentially more time-consuming, as it focused my design skills and taught me some much-needed patience. It will be evident in these hand drawings how I learned and improved with each iteration, where I had motivation and energy, and where it was 3 am and I just wanted to go to bed.
The TR-527 on the workbench, precariously balanced for access to its deepest nooks
An example of an initial reverse-engineering draft schematic. In this case, the analog section of the ADC on the display board.
Broad strokes: Theory of operation
To measure and display optical density, the TR-527 uses photomultiplier tubes (PMTs) as detectors, and filtered, incandescent tungsten lamps as sources. PMTs are conventionally operated with a constant high voltage at the cathode and a grounded anode, where the anode current is a linear function of illumination over a very wide dynamic range. Macbeth employs an unconventional technique, where the cathode voltage is servoed to maintain a constant anode current, and the voltage at the last dynode becomes closely proportional to the logarithm of incident light. A resistor-diode network is used to compensate the deviation from ideal logarithmic behavior of the dynode voltage, which is then scaled, summed, and displayed. This neatly takes care of the necessity to design a logarithmic amplifier in order to convert light intensity to optical density, which itself is a logarithmic ratio of intensities. The service manual for the older, vacuum-tube based, Macbeth TD-401/102 has a wealth of information about this technique and proved useful multiple times during the troubleshooting.





The TD-401/102 operator’s/service manual is great reading, as it goes into great detail about the operation of the TR-527’s older vacuum-tube-based brethren. Select illustrations from the document proved invaluable to understanding how the “modern” unit gets from light and PMTs to optical density.
The photomultipliers and their associated power and measurement circuitry form the core of the densitometer - the capability to convert light intensity into a logarithmic value. The optical design of the TR-527 is what makes this logarithmic value meaningful as an optical density.
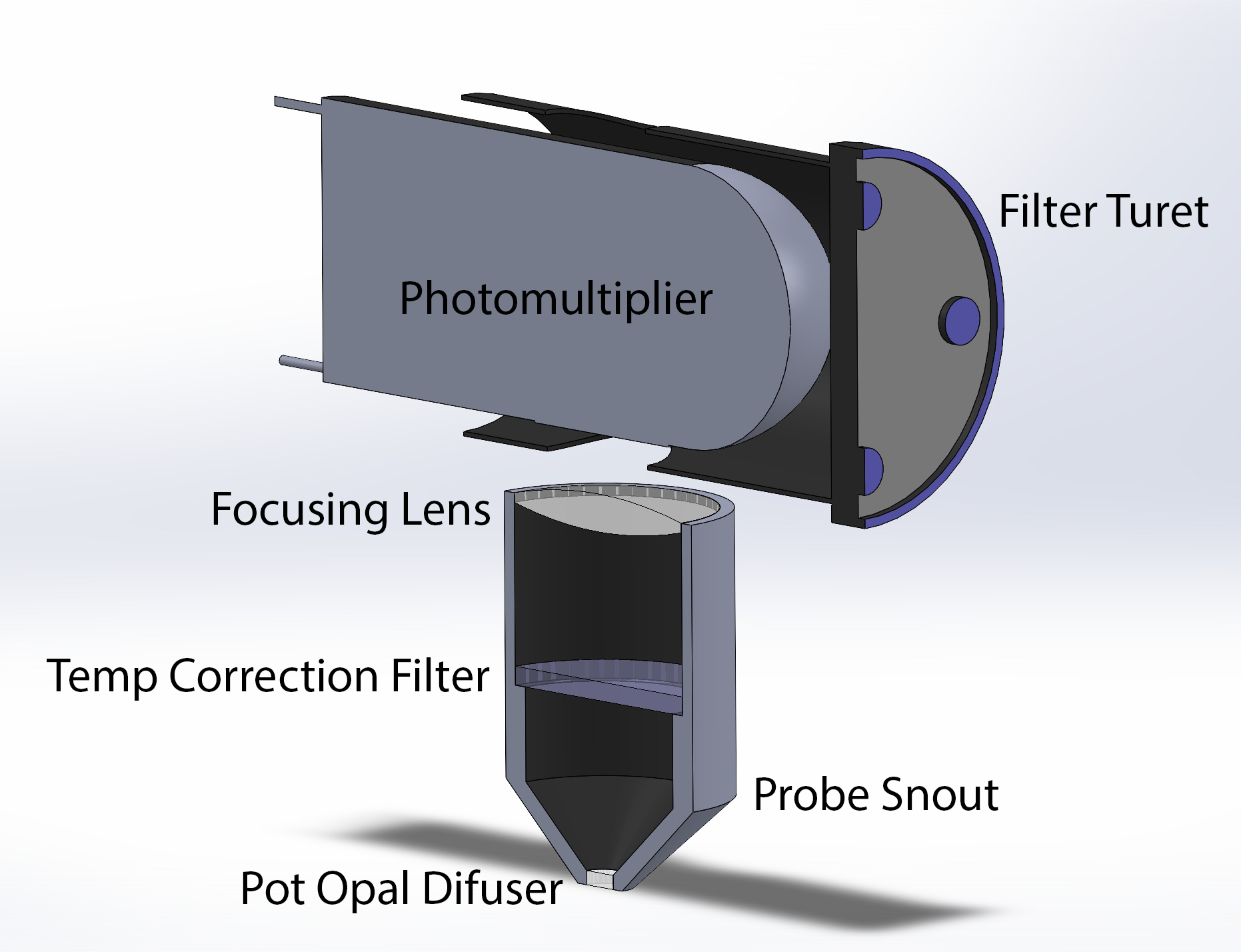
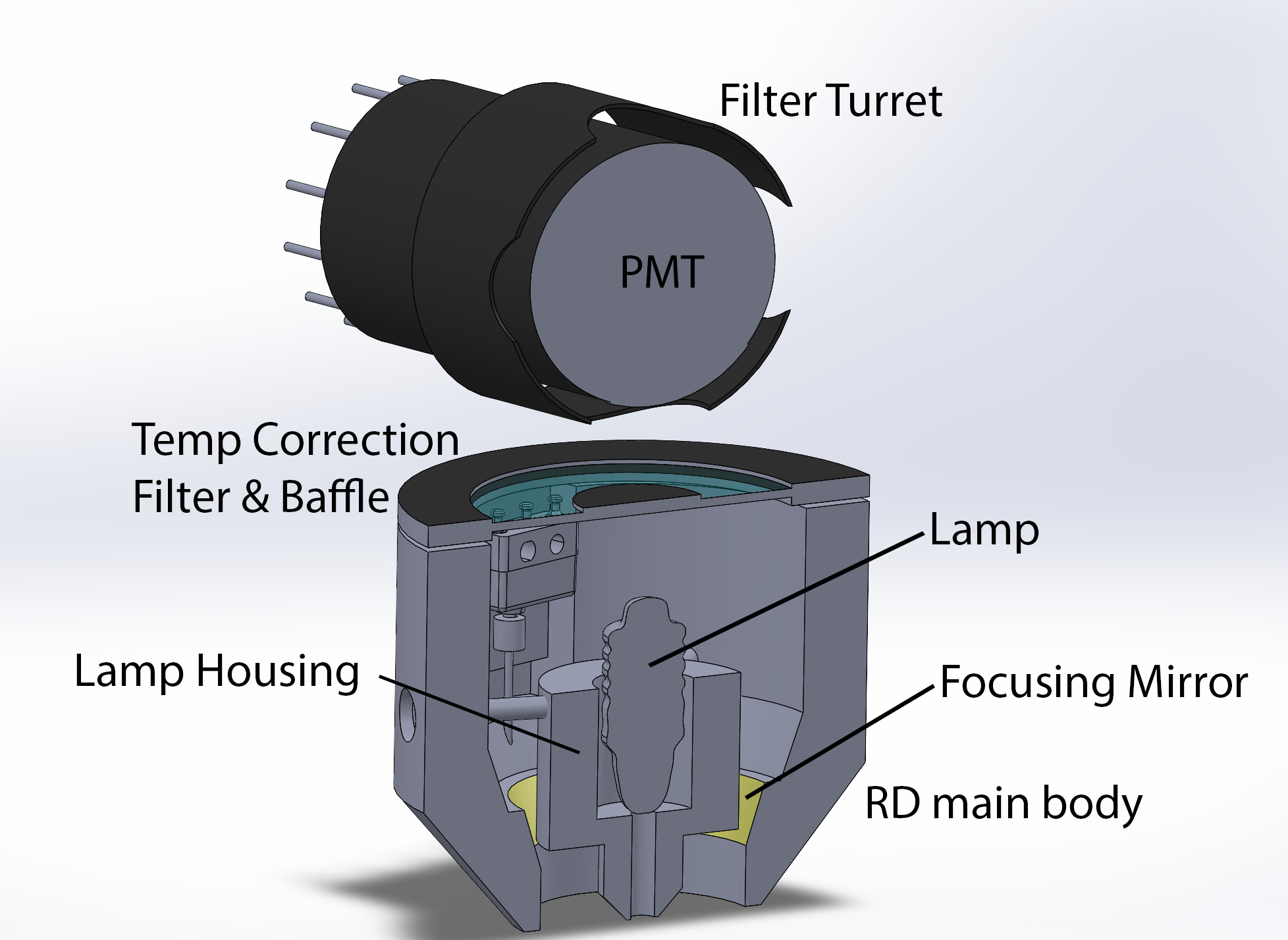
The transmission light pathway is almost identical to that of the TD-102, illustrated in the manual above. Light from a 12V halogen bulb is passed though a heat glass and a condenser lens, which directs it to a 45-degree mirror and focuses the beam onto the sample film at the illumination stage, where the light is restricted by a precision aperture. In operation, the sample “snout” is pressed onto the top of the film surface, mating a pot-opal glass to the emulsion side of the sample. The diffused light passes through a color correcting filter (adjusted to approx 4500K) and is imaged onto the PMT photocathode by a convex lens. Before reaching the detector, the beam is filtered by one of 4 gelatin filters, situated on the filter turret cylinder. This arrangement satisfies the ANSI geometric requirement of directional influx and diffuse efflux of transmission density measurement (aka “diffuse density”). The half angle of incident flux is determined by the size and location of the 45-degree redirecting mirror. I modeled-the TD probe assembly in CAD (not to scale, however) and anyone interested can view it here as a 3D PDF (open using Adobe, not in-browser). There are two built-in views - a full external one and a section view to see the light path better.
Not all light is redirected and the stray beam is scattered within the compartment below the illumination stage, exiting the instrument through the annular opalescent stage plate, in which the sample aperture resides. This provides backlight for manipulating the sample to the desired position when using the densitometer. Unlike previous models, the TR-527 regulates the power supplied to the light source to maintain constant intensity. A selenium cell placed in proximity to the halogen lamp is used in a feedback loop to control the voltage on the lamp such that the light incident on it is constant. This corrects for voltage fluctuations on the supply, as well as aging and darkening of the bulb. It also ensures that the maximum light flux reaching the PMT with no sample film still maintains the PMT and circuitry in their linear, corrected regime of measurement. An additional attenuator can be placed in the light path before the sample aperture, consisting of wire meshes with varying density, which provide a wavelength-independent reduction of flux, to be used when the aperture is increased in size.
The reflection measurement optical system has fewer components and has similarities to the design illustrated in FIG 1 of US3244062 by Monroe Sweet of G.A.F. The RD head consists of two coaxial bodies, with the inner cylinder suspended in the center of the outer body by three mounting screws (CAD mock-up as above here). The inner tube houses a 3.7V 1W tungsten bulb with integral focusing lens, which emits light though a narrow cavity and onto the sample, when the RD head is in its measuring position. Reflected light is collected and focused by an annular mirror in the outer cylinder. In the TR-527, this mirror consists of a precision ground and polished metal surface of the housing itself. The focused beam passes through a color correction filter and one of 4 gelatin filters (identically constructed as in the TD head) before reaching the RD photomultiplier. This arrangement is consistent with the geometric requirement for reflection densitometry for a focused influx and efflux collected within an annular cross-section of defined angle. The angle is determined by the physical construction of the RD housing, the size of the reflective annular mirror, and additionally by optical baffles in the light path. The light source is not regulated in the same way as for transmission mode. The miniature lamp is supplied from a 5V rail via a ballast resistor, and is operated at approximately 1.8-2.0 Vdc. This greatly reduces its intensity from nominal, lowers its color temperature, but importantly, extends its life exponentially. Or such was the design intent, since the lamp is soldered directly into the brass inner housing, and sealed generously with black silicone, clearly not a user-replaceable part, unlike the TD halogen lamp, whose replacement is described in the TR524(7) manual. This lamp had failed in my unit and was a source of great frustration. Luckily, compatible bulbs (E10, 2.2 or 3.7V at 1W) are available online. However, I had to purchase about 10 pieces and select an appropriate unit with a suitable focal distance and centered filament (the integral lens is simply a dab of additional glass on top of the bulb itself and appears to be arbitrary in dimension and focal power).
Such is the opto-electrical heart of this Macbeth densitometer. About 1/2 of the circuitry handles the PMT operation, as well as switching the control and gain between the RD and TD heads during operation. What remains is a way to display the result and a way to “null” the instrument.
Since optical density is essentially a ratiometric measure, “nulling” means telling the densitometer what to use as a denominator, or a reference light flux. For transmission, this can simply be the uninterrupted beam from the light source, or sometimes, the clear base of a film sample. For reflection, it means a surface that diffusely reflects 100% of the light it recieved, absorbing none (as this is practically not possible, reflection is not exactly “nulled”, but rather set to something approaching 0, as will be discussed further). This can be done optically or electrically and every instrument has its own approach to setting zero. The designers of the TR-527 chose an advanced approach, which enabled the user to zero-calibrate every setting of RD/TD and color filter, and then have essentially 8 nulls “memorized” by the unit while it is powered up. I was not aware of this feature and only realized it was explained in the manual on repeat readings (and after stumbling on a kind of digital-to-analog converter with RAM memory while tracing out the schematic diagram…). This ‘zero” implementation is a great exercise in mixed signal design and I will discuss it later in detail. Another great teaching moment in the design of the Macbeth is the digital display and the analog-to-digital converter that drives it. It was yet a late realization that the TR-527 uses Numitron tubes for show its digits. These miniature 7-segment displays are actually 7 tiny tungsten filaments placed inside a vacuum tube and driven at a few dozen mA. They are great, and I love how they look. The ADC is a discrete dual-slope design with some features that puzzled me for a while, pointing to design choices that were probably industry standard at the time, but totally unapparent to an EE in the 21st century.
I am beginning to stray into hard-er core electronics at this point, but to do so without some schematics would be exhausting.
Building Blocks
Above is a distilled schematic of every important element of the TR-527 - a stepping stone to reviewing the entirety of the design in as granular detail as it may befit. For completeness, I have included the optical train for both transmission and reflection, the latter being geometrically accurate, while the former has been condensed and reshaped for compactness.
I have attempted to separate out the functional building blocks of this device which are critical to understanding its operation fully, but also maintain schematic and constructional accuracy. Luckily, the designers at Macbeth (or Kollmorgen) have been kind enough to separate a lot of the functional elements to their own PCB. They weren’t as kind, though, when wiring point-to-point with a rainbow of wires. In tracing out the connections, I ran into a lot of dead-ends or roundabouts. In retrospect, I would have made my life easier if I had broken down the instrument to it’s fullest before beginning RE, since many connections were not obvious beforehand. Mostly the control logic, which is a lot of switches and contacts and diodes and hidden reed switches with hidden magnets,,,
Each functional block has the corresponding PCB numbered as it appears in the instrument, starting from the display at #1 and working backwards through to #4. For clarity, here are their physical manifestations:
At first inspection, I was impressed with the quality of the printed circuit board from the late 70s (most datecodes were in the range of 1978-9). All boards are two-layer with plated vias, all critical areas have a heavy conformal coating and several boards have a a silkscreen overlay with component designators. The hand-taped layout is very consistent and well-planned and the board-edge connectors are generously gold-plated. This outward high quality is mirrored in the circuit design of the instrument, which I will go into now.
Based on the block diagram of the unit and following convention, I think it is most prudent to begin at the power supply and proceed through the light detection, signal processing, nulling, and scaling functions, before finally ending up at the output and display circuitry.
Circuit schematics and detailed operation
Power supply, transmission light source control, auxiliary functions

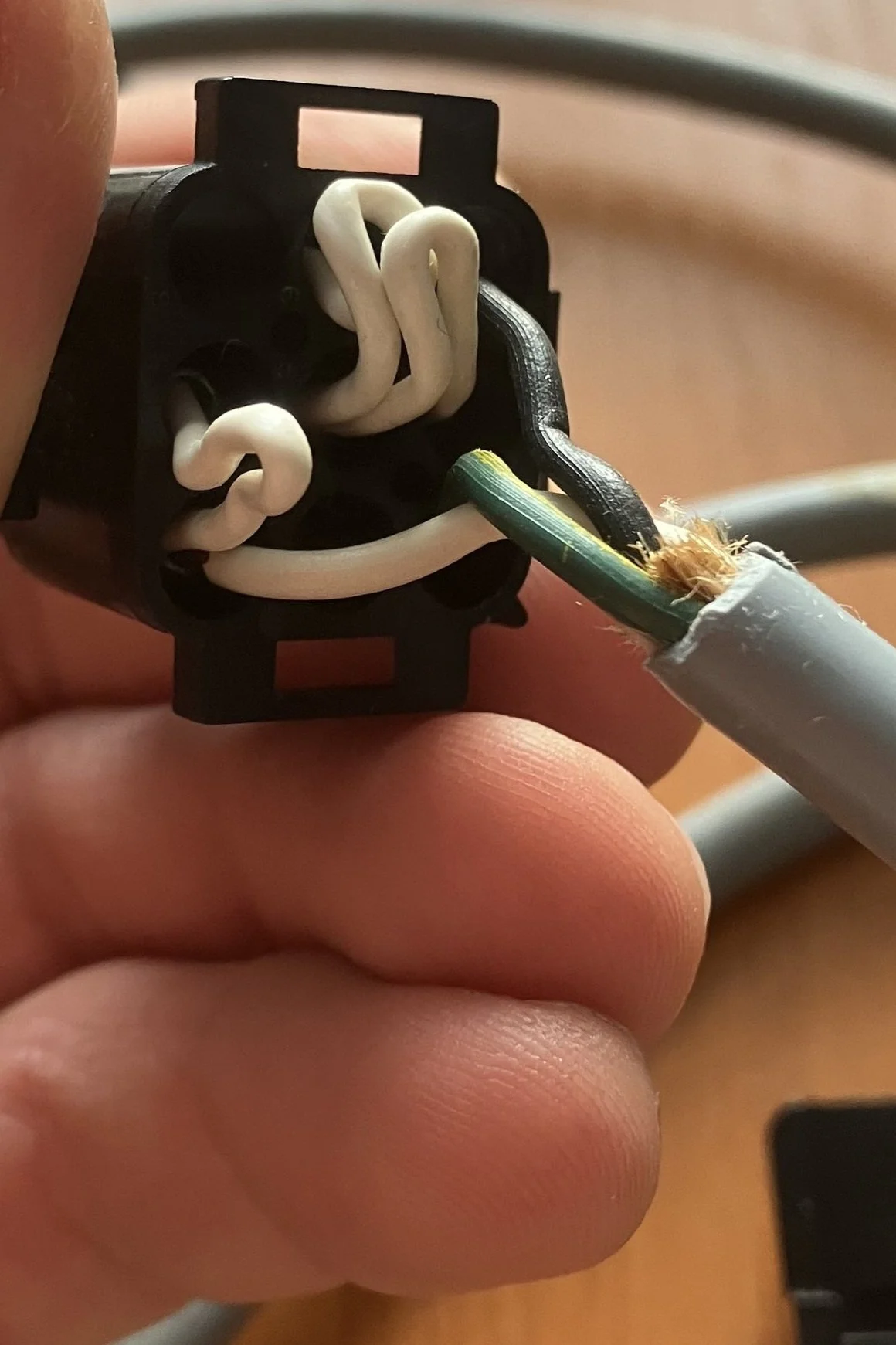
The power supply is a traditional linear supply implemented with an iron-core transformer with windings for multiple voltage operation. To configure 115/230VAC operation, one must disassemble the input “molex”-type connector, since the transformer windings are terminated there. The connections are showed in the figure above, both schematically and diagrammatically in the top left corner. Both primary windings are tapped for voltage adjustment, which is brought out on the top screw-terminal block. Since mains voltage in Bulgaria tends on the high side of 230/240VAC, I opted to use the maximal number of turns, as illustrated. Fuse F1, which is accessible from the outside, should be changed appropriately. A fan in the base of the unit provides cooling for the halogen light and blows air into the upper electronics compartment. The fan is rated for 115VAC and is connected across 1/2 of the primary winding, so for 115V operation, it appears across the mains terminals, and for 230, the primary acts as an autotransformer, dividing the AC input in half to power the fan. The secondary was difficult to trace without desoldering all wiring to the power PCB, so I have taken some liberty in diagramming it. It is possible that the output configuration differs from the schematic, but functionally, this makes no difference to the circuit.
Throughout the board, there is a clear intent to separate analog and digital ground, sometimes to great disservice to the layout, and it begins at the start. One transformer secondary is used to derive the precision +/- 15V rails. The positive reference is derived with the classical uA723 IC, which even today is a venerable linear regulator building block with a stable zener reference (typical tempco of 30ppm/C), current limiting, and built-in output transistor, which in this case is used to drive a larger, heatsinked series regulator NPN device. The negative reference rail is created with an op-amp inverting circuit. Both measured within a few mV of their designed voltages, which speaks well for the stability of the silicon and resistors nearly half-a-century after they were last adjusted!
The second secondary winding is referenced to digital ground. It is full-wave rectified by power diodes located on the radiator and the unfiltered DC is immediately supplied to the TD halogen lamp driver. A complimentary PNP/NPN series-pass element is used to control the current through the filament. The servo loop is under control of a selenium photocell, which monitors the light output through an aperture in the lamp reflector. Its photocurrent is converted to a voltage by a transimpedance amplifier and fed into the summing node of the error/control amplifier, which drives the pass transistors. The setpoint of the servo systems is 5V above ground, implying between 2.4 and 4.5 mA of photocurrent, which is rather hefty, but there doesn’t seem to be degradation of the Se cell and the circuit was in regulation without any adjustments. The control loop is uncompensated, so it most likely works cycle-by-cycle, as the rectified DC reaches a level to produce the setpoint illumination, the servo becomes closed loop and “clips” the pulse peaks to that level.
This attenuated pulsating DC voltage is used to derive the +5V rail, perhaps to relieve the series-pass element from dissipating additional power. The voltage at the emitter of the 2N3055 transistor is fed into a peak detector, comprised of two 3A silicon rectifier diodes and a 2.2mF reservoir capacitor. This is the only place in the entire device, where I observed electronics damage - the two diodes were generously spaced, yet the PCB in their vicinity was charred and even a nearby PNP transistor had signs of heat damage on its encapsulation. During repair, all electrolytic capacitors were replaced, the two rectifier diodes were removed and a BR104 bridge rectifier was fitted in place, along with a token aluminium heatsink. A bridge rectifier, from the perspective of its DC terminals, appears as a parallel combination of two series diodes. Thus, it is hoped that the current will be distributed and the power dissipated more effectively.
Three auxiliary voltages are derived at the power supply unit - a half-wave rectified 10V supply for the numitron display tubes, an unregulated, filtered DC voltage at approx 11V for a large signal relay, and a 15-18VAC AC signal, used by the ADC board for power-line sampling synchronization.
Photomultipliers, TD/RD switching logic, analog frontend and output amplifier
The heart of the TR-527 densitometer consists of its two photomultiplier tubes and the associated circuitry, tasked with producing a logarithmic voltage output, proportional to the optical density being tested.
The PMT’s are RCA-branded, likely a derivative of the classic 931A type, a 9-stage design with side-on window, rated for operation up to about 1000V, or about 100V between each stage. The tubes are operated under a constant anode current regime: a V-I converter, comprised of a discrete JFET input stage (for low input bias currents) and a uA741 opamp produce a voltage proportional to the anode current, which is brought via a shielded cable from both tubes. The resistive T-network can be set to produce a transimpedance gain of approx 10⁷ to 10⁹ V/A. The output is summed with a reference voltage at the inverting input of a servo opamp, which controls a modular, high-voltage DC-DC negative supply (fully enclosed in a hermetic case, no effort was made to reverse engineer its design, but it is most likely a small flyback or resonant topology with a voltage multiplier stage). The negative high voltage is supplied to the PMT cathode and the resistive divider ladder for the dynodes. The resistive ladder is not directly grounded, but is terminated at the so-called “log compensation” network, comprised of twelve matched silicon diodes and potentiometers, acting as temperature-corrected breakpoint compensation for the voltage at the last dynode, which can vary between approx -1V and -8V before the nonlinear correction. The “effect” and “cut-in” controls, as Macbeth calls them, form six compensation points; the cut-in voltage divider determines the dynode voltage at which compensation, in the form of a proportional current, will be summed into the node, and the effect rheostat determines the proportionality factor. This is detailed fully in the older Macbeth manual (an approximate simulation here). The transfer function of the log-correction network as adjusted at the factory for my unit is shown in the graph below. The data was taken by measuring the cathode voltage and the resultant voltage at the Vdy node of the diode-resistor network.
This compensated node is now inversely proportional to the log of light intensity and is fed into the summing junction of an inverting amplifier with a gain of about -4.36. This amplifier also sums the “null” input from the zero DAC and a fixed offset voltage, derived from an adjustment trimmer on board. The output signal is fed into a resistive divider network to be scaled and offset before being passed on to the ADC/Display board. Adjustment potentiometers for TD slope, RD slope, and RD offset are brought out to the back of the unit and are accessible under machined metal caps, which prevent accidental misadjustment. Slope adjustments allow the voltage sent to the ADC to be adjusted between 1/3 and 2/3 of the output voltage. The offset (aka RD “zero”) potentiometer adds a fixed voltage offset to the divided output. This is necessary for zeroing the RD readings if using a calibration standard that is not exactly 100% reflective and is discussed later.
For efficiency, both PMTs are operated from the same control and signal processing circuitry by a somewhat convoluted, but simple control logic. At its core is an 8-pole dual-throw relay (Allied Control Part # TSP163-CCCC-CCCC, 12V) and microswitches positioned in the TD and RD heads, such that when a measurement with either is being carried out, the respective microswitch is activated. In the above schematic, all switches and relay contacts are shown in their resting state. It can be inferred by looking at relay contacts 12-11 (NC) and 21-20(NO) that on powering, the instrument is set up for reflective density measurement.
The negative high voltage for the cathodes is switched through a pair of high-voltage, shielded relays, potentially a reed-type, but I was utterly unable to find any information from the part #, so this is conjecture. In the resting state, the upper relay is turned on by a 2N3392 NPN transistor, whose base is biased high via the lower relay’s coil resistance. Pulling the latter to ground via control relay contacts 21-20 inverts the state of both HV relays, switching PMT operation. Control contacts 26 and 28 ground the end of the unused PMT’s resistive ladder. In the open state, 2000V HV diodes provide protection during switching of states. The control relay is converted into a bistable, latching type, by deriving its supply power from contacts 5 thru 10. The two states of the latch are determined from the states of microswitches MS2 and MS3. If neither switch is activated, transistor MPSA04 pulls the control voltage of the HV supply to ground, disabling it and providing an active-low "STOP” signal, which blocks ADC conversions and the last complete ADC measurement remains displayed. This also directly shorts out the output of the servo op-amp. This oddity was verified several times, and I was concerned that the uA741 was operating in short-citcuit mode for the entire time no measurement was being made, but it seems to cope readily (ironically, the only defective opamp in the device was elsewhere).
The last noteworthy features are the inconspicuous switches RS1 thru RS4 and the small magnets I have drawn next to them. During reverse engineering, when I disassembled the PMT enclosures, I was confronted with odd metal brackets near the PMTs’ input windows (see photo in the introduction, at the far right). The brackets did not support the tubes, though; they had two wires coming out on each side, and were covered in a layer of black RTV silicone. Initially, I ignored them, and I assumed they were modernized versions of the “anti-fatigue” lamp as shown in the TD-102/401 manual, basically a very low-level light that illuminates the PMT when not in use to maintain cathode activity and reduce sensitivity lag. Alternatively, I also thought Macbeth may be using resistive heaters for some arcane PMT stabilization technique. However, as I traced out the circuitry, the nature of the component inside the brackets became more and more a mystery. I could not measure any resistance across the wires, nor was I able to force any current up to a 100V potential thru any of the 4 components. Their connection in the circuit also did not make much sense. Mea culpa, I was too distracted and ignorant to read the manual carefully and realize it was hiding the answer all along; so, I took a scalpel and carved at the silicone until I heard something solid hit the blade - the ampoule of a reed switch! I quickly grabbed a magnetic viewing film and observed the cylinder of the filter turret - magnets! Macbeth was sensing and encoding the position of the filters and passing that to the zero DAC for “null memorization”. Four reed switches and four magnets are used to encode the 8 possible permutations, which are then converted with relay swtiching to a 3-bit number and sent to the DAC board. Lovely.
The “zero DAC”
I find it difficult to identify the correct name of this building block and I have referred to it in multiple ways. It is not exactly a DAC, but it does convert a digital code to an analog voltage. It is not a sample/hold circuit, but it does memorize voltages. It is not a DC servo, but it does attempt to servo an input to zero by controlling its output. Since it has all these features, we should look at the discrete implementations of each of them in this design.
On the analog side, inverting amplifier U209 produces the output voltage based on the state of a switched-resistor arrangement in the upper quarter of the schematic. R207 thru 209 are DIP-8 ceramic networks, branded with a Kollmorgen P/N, with a R-2R-4R-8R resistance ratio. The resistors are switched by the open-collector outputs of SN7489 RAM ICs and biased by resistive dividers from the analog rails. The resultant voltages are additionally weighted and summed into the inverting input of U209. This is the basis for a 12-bit digital-to-analog converter with an LSB resolution of about 6mV and a range of about -5.6V to +12.3V (link to simulation). Three of the 4 available RAM addresses are supplied with the decoded filter selection 3—bit code, so 8 12-bit offset voltages can be made available to the output of the block.
The 12-bit offset voltage code is obtained by the “sample” and “nulling” portion of the schematic. Comparator U210 monitors the output of the PMT frontend summing amplifier and controls a gated oscillator. When enabled, the oscillator feeds a divider cascade, comprised of 3 F7493PC 4-bit binary counters. The outputs of the cascade are directly fed to the data inputs of the RAM ICs. In the idle state, the ZERO node coming from the control logic is floating and pulled up to 5V by R205. DTL inverter U201-1 (F936PC) and inverter-connected NAND gate U202-1 (MC846P) are connected in an OR-node at the input of the gated DTL oscillator, comprised of NAND gates U202-2 thru 4 (link to simulation). When the active “ZERO” button is pressed, the zero line is brought to ground, enabling the oscillator; simultaneously, the negative-going edge is capacitively-coupled into inverters U201-2 and 3, which generate the appropriate reset and write-enable states for the counters and RAM. The WE line is then further toggled at every clock pulse, generated by the oscillator, to store the last incremental 12-bit code.
Every “zero” operation begins with 0s loaded into the RAM “DAC”, which outputs all 1s and all resistors are disconnected. The output voltage thus always begins at its most negative and sweeps incrementally to its most positive. When the summing amplifier output voltage reaches 0V, U210’s open collector output goes high, and inhibits the DTL oscillator, completing the “zero” operation. The input filter C207-R224 adds a small phase shift and U210’s offset balance is adjusted to trip the comparator slightly early, such that the input voltage is precisely zeroed at the end of the null process.
Not all nulls are zeroes, however. As noted, when nulling a reflection density standard, unless it is 100% reflective or close (such as a pure BaSO4 layer or spectralon sheet), any “white” reflectance standard has some RD > 0.00. For example, a Macbeth white plaque may be 0.05 or 0.1 RD units. The zero DAC does not care and will return the offset voltage which brings the output of the frontend to 0.00V. Thus, when calibrating RD, an offset can be set by the external zero potentiometer, away from the control of the zeroing system.
I really enjoyed investigating this circuit. DTL logic was foreign to me, but the Motorola datasheets linked above provide internal diagrams of the construction of most gates and how they can be used in positive and negative logic operation. Noteworthy is the robust input-output structure, which is power-hungry but quite immune to disturbances and allows multiple outputs to be tied together for an automatic “OR” function. The DAC board was the initial inspiration to reverse-engineer the entire TR-527, because it was such a mystery to me what RAM chips were doing inside a densitometer!
Seeing the light: ADC and numitron display
The analog-to-digital converter and display board is the densest design in the entire TR-527 unit and was the most difficult for me to wrap my head around. In broad strokes, a discrete dual-slope integrating ADC is fed from an absolute value circuit, which also provides signal polarity information. The output of the ADC is a 3-order binary-coded-decimal (BCD) code, which is input to BCD-to-7 segment decoders that directly drive the segments of three RCA numitron tubes.
Before reviewing the schematic in depth, I want to provide a primer on integrating A/D converters:
Dual-slope A/D converter block diagram. Retrieved from https://www.cse.psu.edu/~kxc104/class/cse577/11s/lec/lecture/temp/ADC.htm
Integrator output voltage during a conversion cycle. Retrieved from https://www.cse.psu.edu/~kxc104/class/cse577/11s/lec/lecture/temp/ADC.htm
Assume that at time = 0, the integrating capacitor Cint of the model integrating ADC circuit is discharged, its input resistor is connected to Vin and the reset switch is open. The input voltage (negative polarity in the example given) causes a constant current Ichg across the input resistor Rin, since its other terminal is held the opamp’s virtual ground. For Ichg to flow into Cint, the opamp’s output must change at a rate dV/dt proportional to Ichg. When a fixed time interval Tcharge (determined by a known number of clock counts)has elapsed, the control logic switches Rin to a reference voltage Vref of opposite polarity and starts the output counter. Vref causes a known reference constant Ichg to discharge the capacitor. The integrator output now decreases at a known rate dV/dt until it reaches the comparator’s threshold and its output switches states, which causes the control logic to stop the output counter and close the reset switch to ensure the capacitor is discharged for the next conversion. The number of recorded clock counts gives a time Tdischarge, which is directly proportional to the ratio of Vin to Vref. You can convince yourself of this relationship by observing that the charge on the integrating capacitor must equal zero at the end of the conversion:
A dual-slope ADC can be very accurate and linear, because non-idealities in the components are compensated by using the same capacitor to integrate in both directions. Also, it can be seen how such a converter can be easily made to display a voltage directly; let's set Vref to 1V and Tchg = 100 clock counts. For a Vin from 0 to -1V, Tdisch will vary linearly from 0 to 100 counts. so by simply placing a decimal after the first digit, we have a 2.5-digit display of the negative voltage.
In the example above, note that Vin must be a negative voltage and Vref a positive voltage for the integrator output diagram to be correct. Of course, the reverse is also a valid input condition, but the integrating op-amp will ramp down from 0V to some negative value and then up to 0V to end the conversion. However, Vin must always be the same polarity. This will be a problem if we are trying to measure a bipolar signal, such as the optical density output of the PMT frontend, which can be negative or positive, depending on the zero DAC offset and currently measured light intensity.
Let’s follow the Vin voltage along its signal path in the TR-527’s adaptation of a dual-slope ADC. The input voltage is first R-C filtered and then fed into an absolute-value amplifier comprising op-amps U105 and U114. The latter is a simple non-inverting follower (R138 provides bias current compensation for the input-filtering R139), so the input appears buffered at the input of U105, configured as an inverting amplifier of gain -1 and also at the collector of Q105, a small-signal NPN transistor. Observe that a signal diode is placed in series with the feedback resistor of U105; for positive input voltages, U105’s output is driven negative to maintain its inverting input at virtual ground and the voltage at TP3 is thus the inverse of Vin. For negative Vin, U105’s feedback loop is interrupted and its output saturates to the positive rail. This causes both base-emitter and base-collector junctions of Q105 to be forward-biased; Q105 appears as two forward-biased diodes, connected in series opposition. Therefore, the voltage appearing at Q105’s collector is mirrored at its emitter. Since the two PN junctions are on the same die, their forward-bias voltages are inherently compensated. One can also view the NPN transistor as operating in its saturation region, acting as a switch, but we generally try to avoid forward-biasing the base-collector junction. This voltage switching technique was unknown to me and I only understood the principle after simulating the circuit. It is actually a pretty clever way to block or pass a signal with fidelity without resorting to JFET or MOSFETS.
U105’s output is also used as a polarity indicator - it drives Q106, whose output is fed to a type of S-R latch formed from the 4 NAND gates of U115. The latch is reset at every master reset clock(discussed further in a moment) and then set if the input signal is positive; its output controls the vertical numitron segment to form the + sign on the display.
The input signal has now been converted to its absolute value and inverted; it can now be presented to the input of the integrator via R101 and R102. Between the two input resistors sits Q101, which can rudely disrupt the input voltage by forcing the node to 0V (and forcing the current through R102 to be exactly zero, since its other end is at virtual ground). This is again accomplished by the PNP transistor not quite being used as such: its base is normally pulled to the -15V rail, forward biasing both junctions and blocking the input signal. When a 5V digital signal is applied to the “SIG” line, the base is driven positive and the transistor is fully-off, allowing the signal to pass through. One can imagine that a NPN transistor, configured in the usual common-emitter arrangement, would have done the same job, but there would always have been some tens of milivolts collector-emitter saturation voltage.
The Vref voltage (approx 6.0V) is derived from the analog 15V rail via a divider and is fed to the integrator using the same block-or-pass switching technique, controlled by the “REF” line. The integrator consists of U101 and C101, a 47nF film capacitor. Q103, an N-channel JFET serves at the reset switch, which ensures the capacitor is fully discharged at the beginning of every conversion. Comparator U102 monitors U101’s output and compares it with its virtual ground node to determine the end-of-integration. I’m not sure why the designer chose to connect U102’s non-inverting input to virtual ground instead of the actual ground, but I presume it is to account for offset due to U101’s Vos and the voltage drop across the bias compensation resistor.
Note: U111 should read “U110”. CLKA, SIG IN/REF IN, Vint, and COMP OUT timescales are expanded for clarity - the full run-up and run-down occur in a few milliseconds, compared to the hundreds of ms between A/D conversions.
This is where our analog pathway terminates, charging and discharging C101. To better understand the digital pathway, I have drawn a timing diagram of the relevant signals involved in the conversion.
Everything begins with a 12VAC signal, derived from the mains transformer’s secondary, and fed into Q110’s base; a roughly symmetrical 100Hz 5Vp square wave appears at the collector. This “synchronization” signal is AC-coupled into the gate of Q108, a programmable unijunction transistor (PUT), configured as a trigerrable monostable oscillator with R128 and C108. Q108 remains in the off-state until its anode voltage exceeds the gate voltage by about 0.7V. If we assume an initially charged C108, both A and G are sitting at the positive rail, until a negative-going edge is AC-coupled via C111, triggering the PUT, which discharges C108 into R134, and turning Q109 on. When C108 is discharged to about 0.8-1V, Q108 shuts off, allowing R128 to charge it back up. The PUT will not trigger again until C108 is charged and another negative edge is coupled from the synchronization signal. The 220k-1uF RC time constant implies a frequency of about 5 or 6 Hz, depending on the mains frequency. The resultant “master” clock at Q109’s collector appears as a square wave with a duty cycle of 99% (width determined by the RC constant of C108 with R134, about 3ms) and is used to reset the integrating capacitor and ensure the Vref input is also blocked during the reset. One of U103’s NAND gates inverts the “master” clock for use within the rest of the circuit as a “master reset” for the BCD counters, the polarity indication latch, and the signal switching latch.
The “control” logic, at its heart, is a simple S-R latch formed from two of U103’s NAND gates. At the beginning of a conversion, a negative-going edge from the “master reset” is AC-coupled into the latch, setting its Q output high. This is the “SIG” line, which unblocks the Vin signal. The last of U103’s NAND gates is configured as an inverter, which drives the “REF” line low, blocking the Vref reference signal. The integrator now sums the unknown input current and its output goes positive. Comparator U102’s output, which is at ground, is fed to one of U104’s NAND gates, and so is the S-R latch’s complementary ǭ output. Since both are “0”, U104-1’s output is high and enables a gated RC oscillator formed from the remaining three of U104’s NAND gates. The oscillator generates a “fast” clock at a few hundred kHz, which is fed to three cascaded SN7490 decade counters. The integrator continues to integrate the input signal until U110’s Qd output toggles after 1000 “fast” clock ticks, which causes a negative-going AC edge to be coupled into the S-R latch’s R input, resulting in the “SIG” line going low and the “REF” line - high. The integrator is now set up to “run-down” with the reference current. The “fast” clock oscillator remains enabled and the decade counters overflow, resetting the count to“0”. The integrator’s output is now negative-going and once it reaches or slightly overshoots 0V, comparator U102’s output goes high. With logical “1”s on both of its inputs now, U104’s NAND gate 1 goes low, stopping the fast clock. The counters are blocked at a count representing Tdischarge. The three SN7446 BCD/7-segment decoders drive the numitron display to show the resultant count. In fact, the decoders are not latched or disabled during the “run-up” or “run-down” integration, but since these occur in the order of a millisecond or two, the display’s latency prevents the count-ups to be displayed.
The “STOP” input from the TR-527’s control logic is connected to Q108’s anode via a rectifier diode. When either of the measuring heads is activated, the STOP line is high, allowing Q108 to oscillate. When a measurement is completed and the measuring head is released, the STOP line goes low, discharging C108 and stopping the ADC at its last completed reading, which remains on the display indefinitely, or until a new measurement is carried out.
The ADC is synchronized to the mains frequency to reduce interference, since conversions are deterministically positioned in the AC cycle and are always carried out around a zero-crossing point. This technique is also used in higher-end bench DVMs, where one can configure a NPLC (number of power line cycles) integration time, slowing down the A/D converter, but gaining more resolution from the decreased noise.
Three potentiometers are available to adjust the performance of the ADC. One is an offset control for the polarity indicator, which adjusts the switchover between + and - indication. Another sets the exact value of Vref and so adjusts the slope of the A/D converter. The final pot trims the offset of the integrator op-amp and adjusts the A/D “zero”.
This sums up the final building block of the densitometer. I found reverse-engineering this board very engaging and I was impressed at the “minimalist” design that works surprisingly well. I was able to trim the ADC to read a bipolar DC voltage to within one count.
I have compiled the schematics, pictures, and some other useful notes into a PDF for convenient use and better resolution.
Keen-eyed readers might observe that I have omitted a part of the PCB in the schematic - it is three ICs short! They are two DTL hex inverters and an unpopulated 16-pin DIP socket. The 12 inverter inputs are directly connected to the 12 (3xBCD) data lines from the counters to the decoders and the outputs connected to pins on the unpopulated socket. This is almost certainly a provision for the “digital output” upgrade option, as outlined in the user manual. Images from other auction listings give us an idea how this upgrade looks externally:
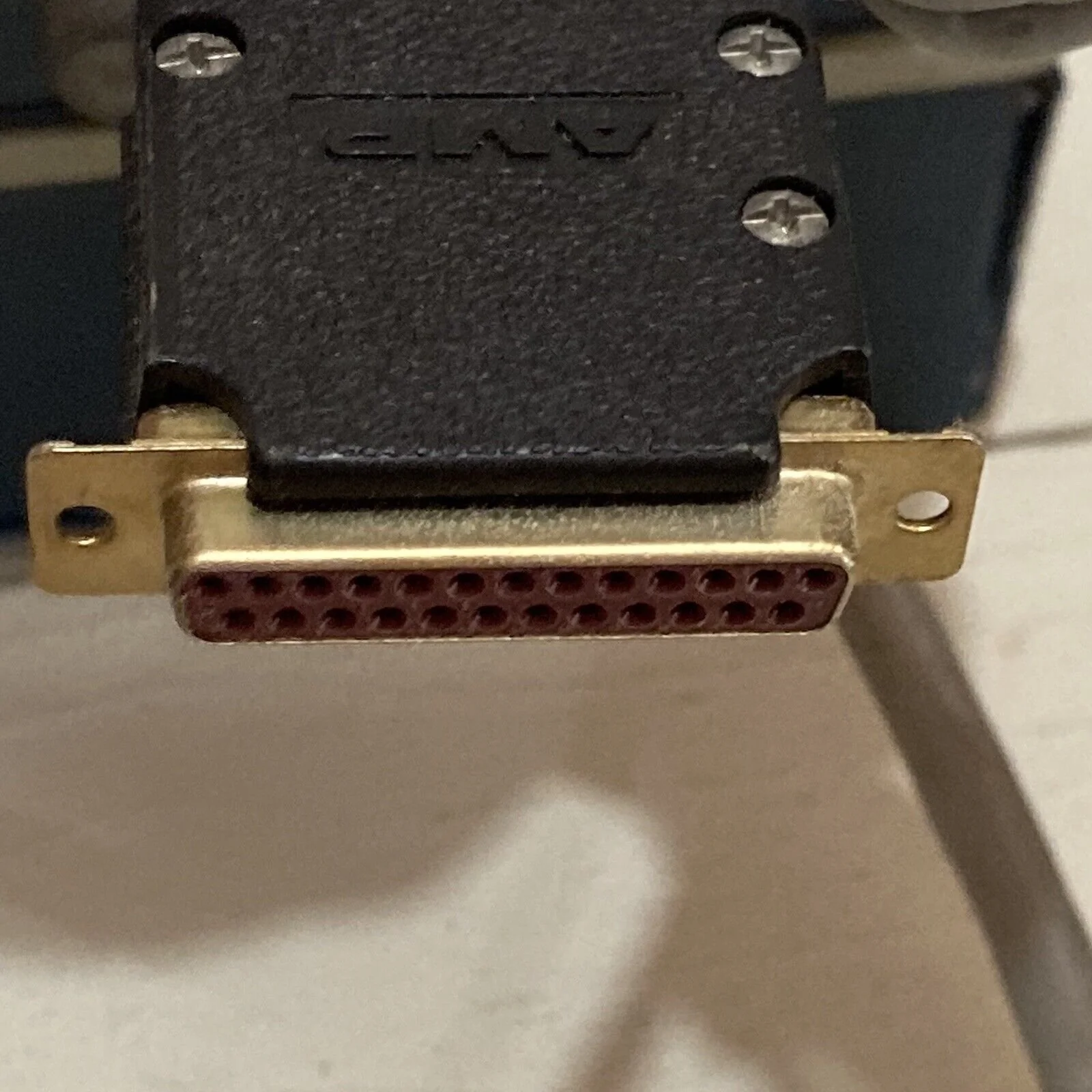

The DB-25 connector suggests that the inverted data lines from the ADC are brought out in a parallel configuration, along with the STOP signal and the 3-bit filter encoding bits. Perhaps there is additional circuitry, which can be populated on the free space on the Zero DAC board, but I wouldn’t know (unless I bought another Macbeth in need of restoration… but I’d rather not deprive another enthusiast of such a pursuit:).
Now what? Repair and troubleshooting
After elucidating in detail how the TR-527 functions, it will be easier to explain how my particular unit was faulty and how I located and fixed the problems.
For starters, one very obvious issue was that the RD head was inoperable - its probe snout did not illuminate and actuating the RD microswitch did not reset the main unit to RD mode. The RD illumination bulb measured open-circuit, so a replacement was in order. Luckily, E10 1W miniature bulbs are still manufactured and available:
I was also able to locally source NOS E10 lamps with lenses, but with a 2.2-2.5V/0.5-6W rating. In theory, these bulbs can also work, with a modification of the series ballast resistor. As mentioned above, the quality of these lights varies, so I recommend purchasing at least 5-10 and selecting the brightest and best-focused one. Replacing the bulb is a hassle, since it is directly soldered to the inner brass snout and then liberally covered in black silicone and optical black paint. I opted to omit the silicone and after positioning the bulb and soldering it in place, I used a matte-black enamel paint to cover all surfaces.
The other broken component in the RD head was the main RD microswitch - a Honeywell 1SX12 precision miniature switch, which retails for $20. Luckily, cheaper alternatives with the same form factor are available, and I was able to substitute a locally-sourced sub-dollar part successfully. I think the choice of microswitch was justified, since it must have a low mechanical hysteresis, so that the RD head is activated exactly when it is firmly pressed onto the sample, and then the switch has to release as soon as the head begins to move away from the surface (such that the ADC can be stopped before an erroneous reading can be recorded).
These fixes recovered RD functionality, but the unit still could not be zeroed. Armed with the full schematics, I began tracing the zeroing pathway and verifying functionality. The culprit was quickly identified as the Zero DAC inverting op-amp, which was nonfunctional, railed to the positive supply (hence applying a large negative offset to the output, keeping the display maxed out). Ironically, the op-amp is an LM741, probably the most popular amplifier IC in the past century, yet I was unable to find it locally, even Soviet era substitutes. I eventually ended up using an OP-07 precision amplifier as a replacement, and that worked fine, restoring zero functionality.
Although there were no other functional issues present, as I began testing the unit, I noticed the TD measurements being erratic and unstable. Nothing in the electrical pathway seemed off, however, as the same circuitry is used for RD measurements, and they were consistent and stable. Disassembling the TD probe snout to check the optics, I discovered the problem - the glass color-correction filter and the focusing lens in the probe snout were contaminated with a white crust! It didn’t appear as fungal growth, but more like caked-on salt-water or other inorganic matter. It dissolved in water and a wet towel cleaned the convex line just fine. However, the blue filter sustained damage to its coating, and one of its surfaces was heavily pitted, causing the filter to act like a diffuser, scattering the light that should be collected by the lens. Not only does that decrease the light available for measurement, but it likely affected the measurement geometry. I considered polishing the filter, since it was made from dyed glass, and removing a few parts of a millimeter would not have affected its absorption considerably. However, the pitting was substantial enough that mechanical polishing would have been a long and tedious process.
I tested a potential alternative, which worked surprisingly well. I had available a UV-activated crystal epoxy resin (in one of those quick-fix pens with a UV led on the back). Initially I attempted to apply a layer of epoxy on the rough surface and curing it directly, but that resulted in an uneven, curved surface. After removing it with a solvent, I tried to place a small glass side on top of the epoxy before curing it. This resulted in good optical clarity, since the resin has a very similar refractive index to the filter glass. However, attempting to remove the glass slide, which I had pre-treated with silicone oil as a release agent, required heating the assembly and trying to pry the two glass bodies apart. This was not only dangerous, but actually caused the epoxy layer to delaminate from the filter, not the glass slide. Finally, I used a LDPE platic lid as the “capping” surface. Although not optically smooth, the lid allowed me to expose the epoxy layer and then separate the filter very easily, resulting in a transparent, “nearly-optical” grade finish. Since the filter does not have to provide imaging quality, just not disperse the light, I settled on this solution.
All components of the TD snout were cleaned in warm water and detergent, with special attention to the pot opal diffuser, which had accumulated dirt and grime over the years. After reassembly, density readings were consistent and the full operating range was restored.
This concluded the troubleshooting of the TR-527, as its full functionality was recovered. I went one step further by replacing all electrolytic capacitors, aluminum and tantalum, with new ones and made a modification on the power board, as outlined above, to prevent overheating of the power rectifiers used. One additional “upgrade” I made was prompted by the availability of a hole for a fourth “calibration” pot on the back of the unit. This hole perfectly accommodated a 4-pin DIN female connector, which I installed and connected the pins to analog ground, Vout, a signal indicating RD/TD mode (labelled HT_SW in the PMT frontend schematic) and the STOP line. Potentially in the future, I may create an external uC interface, which would allow me to quickly make measurements and directly record the results (with however many digits I decide) into a spreadsheet.
Making Measurements Meaningful: Calibration
With the Macbeth now in full working condition, I had to tackle making the numbers on the display be meaningful measurements of reflection and transmission density. This meant adjusting the CAL and ZERO adjustment potentiometers on the back of the unit. The Macbeth manual provides a calibration procedure, which involves using a reference step wedge and reflection plaque and trimming the densitometer until the readings match the calibration values given.
Since I did not receive either a TD or RD calibration standard, I had to figure out an alternative method to trim the TR-527. I also wanted to go one step further and verify that the half-century-old electronics were still doing their expected job, and correctly converting the linear light input to a logarithmic representation of density.
If we trace the full signal path, in both the optical and the electrical domain, it may look something like this:
Light Source -> Influx Optics -> Sample -> Efflux Optics -> Light Conversion -> Logarithmic Conversion -> Scaling and Offset -> Signal Visualization
On the optical side, we have mostly linear modification of the signal - reflection, focusing, attenuation, which are defined by the light path and its geometric construction. As previously discussed, the construction of both RD and TD measurement heads is consistent with the requirements for photographic density measurement, and Macbeth is a known, “industry-standard” instrument manufacturer; thus, whatever happens to the signal up to the light conversion steps can be taken as “standard”. Things deviate into uncertainty in the next two steps. The PMTs in the TR-527 are operated in a nonlinear fashion, and the pseudo-logarithmic output is further corrected by a discrete compensation circuit, which must be manually adjusted using 12 trim-pots so that the output becomes a linear function of density. The last two steps are once again linear transformations. This is important, as “linear” functions can be adjusted, but any deviation from logarithmic behavior cannot be “calibrated” out by using the user-accessible controls on the back of the unit and would require a much more tedious trim of the break-point compensation network.
My initial attempt tried to relate density measurements from existing densitometers. I have a collection of film test strips and an uncalibrated Stouffer step wedge, which have been measured using my homemade transmission (articles on its construction still in progress..), as well as several inkjet prints, which have been measured using a Datacolor Spyder printer calibrator spectrophotometer. I have also prepared a thick layer of precipitated barium sulfate (BaSO4, aka baryta), which should have a flat diffuse spectral reflectance approaching 1.0 (closer to 99.5%). By measuring known densities and adjusting the slope (“CAL”) potentiometers on the Macbeth, I was able to roughly calibrate the unit to my previous “known” devices. This was OK for a first-pass calibration, but the result can be only as good as the reference source. For example, I noticed a deviation from linearity when calibrating transmission density. I would zero out the unit, then select a relatively high density, at which to calibrate the unit, then take measurements between the two extremes; theoretically, the Macbeth TR-527 readings would agree with the prior data or at most have a constant offset. This was not the case:
Macbeth TD readings vs Step Wedge readings taken with my existing densitometer. Deviation is calculated as deltaOD.
Although it was possible to set the TD slope to agree within a few %, it can be seen that the OD readings begin to deviate by up to 0.06-0.07 units at higher densities, which is substantially higher that the 0.02 “accuracy” spec of the Macbeth. My homemade densitometer is photodiode-based and uses an off-the-shelf logarithmic amplifier to calculate optical density, so its electronic side of the signal chain can be trusted. However, its optical pathway is substantially different from Macbeth’s - TD is obtained with diffuse influx and semi-specular efflux mode (no imaging optics involved). Since the world isn’t ideal and geometric considerations matter, factors such as the Callier effect and transition losses cause the observed non-ideality between the two units. Thus, my existing densitometer could not be a true “standard” for calibrating the Macbeth device, because they are inherently different in measurement configuration.
So, what is one to do? Luckily, since optical density is a ratiometric quantity, we do not strictly need to use artifact calibration (i.e. a purchased or measured sample). We can assume we trust the optical pathways (again, as they are designed and constructed by Macbeth specifically for photographic density measurement) and we only want to verify that the electronics do what is expected of them. We can achieve this by substituting the entire electrical pathway with a “known reference” design. Photodiodes are remarkably linear transducers, capable of converting light to electrical current over 5,6 or even more decades. This current can be amplified and directly measured with a calibrated digital multimeter and the logarithm calculated numerically. Alternatively, a calibrated logarithmic amplifier can be added to the signal chain to directly give density readings. Since I have previously built and calibrated a discrete log amp (link to come), I opted to use it. A logarithmic amplifier outputs a voltage that is proportional to the logarithm of the ratio between the input current and a stable reference current (set to 1uA in my design).
To carry out the calibration by substitution, I removed the filter turret to gain access to the PMTs and positioned a BPW21R color-corrected silicon photodiode immediately below the light-entry window to the phototubes. The current from the detector is carried by a flouropolymer coaxial cable, through a light-tight metal cap, which replaced the filter turret, and passed into the shielded log amplifier. The setup for TD calibration can be seen here:
Transmission density calibration by intercepting the light path with our own circuit. A light-tight metal cap replaces the filter turret and a shielded PTFE cable takes the photodiode current to a custom logarithmic amplifier, seen to the right. Behind it is an isolated bipolar power supply and off-frame is a Fluke 87V DMM measuring the output voltage.
Reflection density was likewise measured. I have to make a few notes on this calibration technique. The photodiode is relatively large (7.5 sq.mm. die area), but still a small fraction of the PMT window size. This is OK, because, as long as the position of the diode doesn’t change during measurements, a fixed percentage of the input light will be measured, only contributing an offset in OD. The filter turret is removed, so the PD will read the unfiltered density. This is also OK, because the diode has a wide spectral response, which is similar to the PMT’s, and any filtration also presents linear attenuation of the optical density. The latter is true for neutral density samples, with significant leeway - the bluish base of a film strip or an inkjet print with some color cast are adequate for the calibration. Finally, I allowed the TR-527 to warm up for at least 15 minutes before taking the final measurements and making the final adjustments. Although the manual claims an one can immediately start measurements at power-on, the unit does drift with temperature and considerably warms up during operation.
Several densities between 0 and 3 were first measured with the photodiode setup and the corresponding logarithmic voltage recorded. Then, the unit was returned to normal operational mode, and the highest measured density was used to calibrate the slope. Then, the intermediate densities were measured and recorded. Plotting the results gives us the final “calibrated” response of the TR-527:
Not bad at all. In fact, deviations are within the error budget of the setup, and are basically within the stated accuracy. It was very satisfying to see how the two measuring systems, which are so fundamentally different from each other in operation, still yielded near identical results. As a bonus, the TD and RD sample densities measured during the test are now themselves “calibrated” to the photodiode circuit and can be used to spot-check the Macbeth in the future. The only true “artifact” calibration standard is my baryta plaque, which can be used to verify or set the RD “zero” of 100% reflection.
And with that, the TR-527 earned itself a position on the shelf in my darkroom.
Conclusion
I’ll keep it brief (because the rest sure wasn’t): this was fun. It was fun to dissect the Macbeth, it was challenging to reverse engineer its schematic and operation, it was satisfying to fix it and see it back in operation and in spec. I also enjoy describing how I got to this point, and I acknowledge I’m neither a good technical writer, nor an efficient narrator, but I know that even if one reader finds my verbose ramblings edifying or of practical use, the effort would not have been in vain.
-Niko